- Mar 3, 2020
- 1 min read
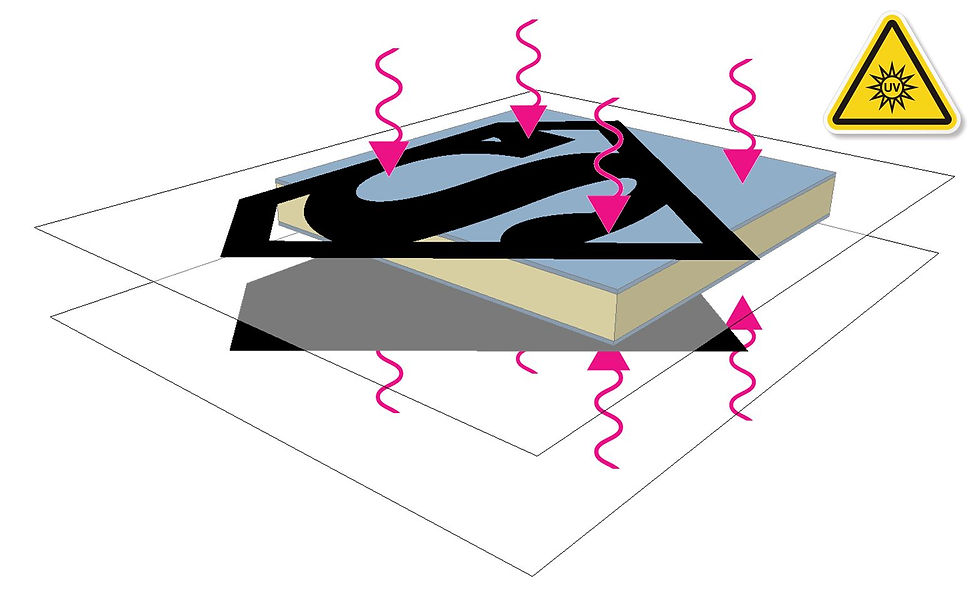
The technical description and drawings:
The double UV light box is made of 12 actinic 8W Philips tubes (16 mm diam, 29 cm length), 6 tubes on both sides.
The box will be made of 10 mm thick ply wood and 5 mm thick MDF.
The front control panel will be made of 2 mm thick aluminum plate.
It will include all the necessary electronics to automatically control the expure time.



The box:
Both the ply wood and the MDF are cut according to the technical drawings.

They are then screwed and glued together to create the two sides of the UV light box.


The inside of the boxe where the 12 actinic 8W tube will be attached is made of 2 mm thick styrene.

The 24 plastic tube holbers will be fixed (not glued) inside the 24 holes in the styrene plate.



The lights:
12 actinic Philips tubes, 24 plastic tube holders and 6 converter (1 for 2 Actinic tubes).

This is how the 6 converters are screwed inside the UV light box.

The electronics:
The front control panel electronics is composed of:
1. AC/DC adapter (transformer): Input: 100-240Vac 50/60Hz, Output: 12Vdc 680mA
2. Main red switch ON/OFF with light
3. Trigger button
4. Plug for power supply
5. Adjustable 12v DC digital timer relay control with display

The front control panel made of 2 mm thick aluminum plate.

This is the technical drawing for the wiring between the actinic tubes and the converters.


Painting the box:
First layers of white primer.


Stay tuned as there will be MORE TO COME...